APPLICATIONS FOR BENCHTOP PNEUMATIC PRESSES
We have solutions for many standard manufacturing applications. Our Presses have been designed to be easily customizable and configurable for any project your company requires. If you do not see what you are looking for here, check out our SOLUTIONS or send us REQUEST FOR QUOTE!
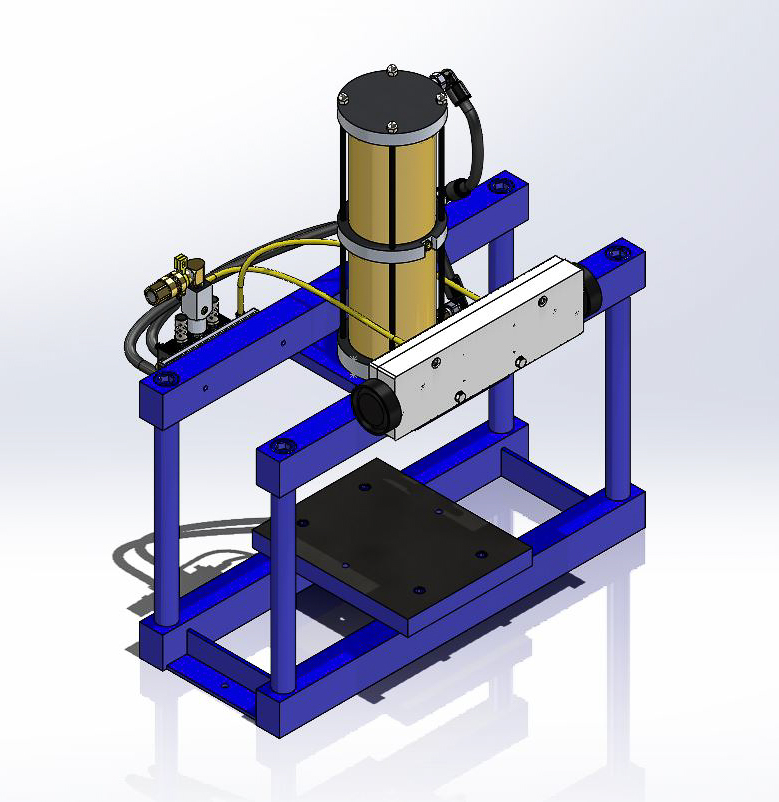
Custom Application Solutions
Presses Engineered For Your Needs
Regardless of your application, Joraco Press Company can provide a pneumatic press or rotary indexing machine that is best suited for your specific project needs.
We have a team of Engineers, Project Managers, Machinists, and tool makers who can design and manufacture custom equipment and tooling. Our facility has multiple CNC Stations and we use the latest SolidWorks CAD software to model your machine alongside your team.
COMMON PRESS APPLICATIONS
Assembling
Compacting
Crimping
Die Cutting
Forming
Piercing
Pressing
Joraco Press Company Designs Dual Press System for Wheel Hub Assembly For Leading Agriculture Solutions Provider
By combining our technical leadership in both pneumatic press engineering and industrial automation, Joraco Press Company built an automated press-fitting system for a leading manufacturer of tractors. This oversized press is engineered to press fit bolts into tractor wheel hubs with high precision.
This assembly system that includes two 8 Ton HYDRO-AIRE® Series hydro-pneumatic presses, incorporates an electric servo motor mounted on top of a pneumatically powered linear slide and an optical sensing system. As the operator loads the hub into the press with pins loosely inserted in the desired locations and activates the system, the linear slide moves the wheel into position. Guided by optical sensors, the servo motor rotates the wheel hub until one bolt is accurately located under each of the two presses. As the bolts are held in perfect alignment, the presses actuate simultaneously with a precise amount of force to insert them into the hub. The motor then rotates the next two bolts into position, and the process is repeated until all the bolts are inserted. The slide then retracts, and the part is manually ejected.
For maximum strength and rigidity, Joraco Press constructed the press from a combination of cold rolled steel and tool steel. With a footprint of only 45.0″ long x 24.0″ wide, the machine occupies just 7.5 square feet of floor space. A safety light curtain was integrated that protects operators from injuries related to machine motion. To learn more about this system or our custom solutions for product assembly, contact Joraco Press Company directly.
Riveting
Rivets are permanent fasteners that feature smooth cylindrical shafts with a head on one end. Manual installation requires the use of pre-punched or pre-drilled holes into which the rivet is inserted. Once it is in position, its exposed end is hammered to secure it in place. Riveting press machines serve as a modern alternative to manual riveting, allowing for easier, faster, and more consistent installation. They are available in many variations—such as manual feed or automatic feed—to suit different manufacturing applications. For Riveting Applications, we provide tubular/eyelet rivet machines built around our standard line of TOGGLE-AIRE® Series Pneumatic Presses. These machines offer the same reliability and ease of maintenance expected of us and give customers the convenience of interchangeable parts between the rivet machines and pneumatic press line.
Staking
Staking Workstation for Supplier of High Quality Laser Engraved Pet ID Tags
A supplier of high-quality laser engraved pet identification products approached Joraco Press Company about the possibility of furnishing a turnkey staking system for the forming of anodized metal into several specific dog tag profiles.
This turnkey workstation incorporates a staking press with custom tooling; a servo-powered rotary indexer and an air driven ejection system. After the operator loads blanks onto a rotary indexer with custom nests for each of the seven different profiles, the indexer moves the parts under the press where they are staked. Staked parts rotate to the ejection station where they are blown out of the nest by a pneumatic cylinder and into an ejection chute.
We built this automation system for continuous duty operation. At the customer site, it runs 24 hours/day for the mass production of pet identification tags with overall dimensions of 2.5″ in diameter x 0.1″ in thickness. The servo motor on the rotary indexer allows for flexible, high accuracy positioning to obtain repeatable accuracy of ±0.001″ on the finished tags. The customer was so impressed with the speed, accuracy, and repeatability of this system that they placed an order for four additional machines.
Swaging
See MoreCalibrating
See MoreCompressing
Joraco Press Company Manufactures a Hydro-Pneumatic Press for Use in the Pyrotechnic Industry
Joraco Press Company, a premier manufacturer of pneumatic presses, was approached by a company well-known in the pyrotechnic industry to provide a press that would enhance the production of their unique product line. This particular application called for the ability to compress volatile material within a form to a specific density. This is not the first time that an Joraco Press was chosen for an application that called for the compression of explosive material and they were excited to gain more exposure in this field.
Joraco Press's HYDRO-AIRE Series offers clean, reliable and accurate results with presses ranging in capacity from 4 to 30-tons of force. This air-over-oil series is a much cleaner alternative to a hydraulic press and offers the same advantages. It is fully contained with no fluid reservoirs or hydraulic lines, and features rapid advance with an automatic power stroke.
The customer was pleased with the arrival of their 8 ton HYDRO-AIRE Series Model HP8 press. Not only was it delivered in the nick of time, but it also worked out of the crate just as it was intended to do. They received our press with a narrow window of time before they were schedule to meet with clients to test the manufacturing process utilizing it, but their confidence was assured quickly upon its arrival at their facility. Much like our customers, Joraco Press Company also strives to produce high quality products that perform as advertised.
Cutting
See MoreFastening
See MoreHeat Stamping
See MorePress-Fit
Punching
Joraco Press Company used its TOGGLE-AIRE Series Model 3530 pneumatic toggle press and a custom designed punch tool set to help a client with their sheet metal sample packs. Using 2" infeed material up to 24g galvanized steel or .040" aluminum, operators can stamp 2" x 3.5" card sized samples with 1/4" rivet holes to combine a variety of samples. No hydraulics! No electronics! Just a simple air feed and benchtop space. While this version is manually fed with pre-cut stock, the press can easily be combined with feeders, decoilers, and straighteners for automatic punching needs!
VIDEO BELOW
Shearing
Joraco Press Company's Punch & Shear Application Using Servo Driven Feeder
Joraco Press designed and built the fully automated multi-press punch and shear system for the manufacturing of transformer core sheets. It featured two high-accuracy 10-ton TOGGLE-AIRE® Series Model 2530 pneumatic presses, one for punching the hole and the other for shearing the sheet. The primary challenge of this project involved obtaining precise tolerances of ±0.002″ around the burr of the punched hole on the steel sheet. To ensure dimensional accuracy in the customer’s stack core transformer design, our engineers had to design, build, and exhaustively test the punch tools to ensure they repeatably produced holes with the correct size and shape.
Constructed from cold rolled steel for strength and rigidity, the automated punch and shear system features a space-saving 29.5″ long x 30.75″ footprint. Along with the two presses, it incorporated a servo feed that delivers precise positioning accuracy and enables the press to produce consistent parts with close tolerances at fast operating speeds. The punch and shear system also included an integrated PLC system that was fully programmed and ready to run as soon as the customer loaded up the material.
Joraco Press Company supplied this automated fabrication system with a precision sharpened carbide tooling package. The tooling successfully obtains precise tolerances, and with carbide’s ability to maintain its cutting edge, even during high speed punching, it produces accurate parts over long production runs.
Marking
Vintage Joraco Press TOGGLE-AIRE® Series Marking Press on Science Channel's How It's Made:
Stamping
Assembling
Compacting
Crimping
Die Cutting
Forming
Piercing
Pressing
Joraco Press Company Designs Dual Press System for Wheel Hub Assembly For Leading Agriculture Solutions Provider
By combining our technical leadership in both pneumatic press engineering and industrial automation, Joraco Press Company built an automated press-fitting system for a leading manufacturer of tractors. This oversized press is engineered to press fit bolts into tractor wheel hubs with high precision.
This assembly system that includes two 8 Ton HYDRO-AIRE® Series hydro-pneumatic presses, incorporates an electric servo motor mounted on top of a pneumatically powered linear slide and an optical sensing system. As the operator loads the hub into the press with pins loosely inserted in the desired locations and activates the system, the linear slide moves the wheel into position. Guided by optical sensors, the servo motor rotates the wheel hub until one bolt is accurately located under each of the two presses. As the bolts are held in perfect alignment, the presses actuate simultaneously with a precise amount of force to insert them into the hub. The motor then rotates the next two bolts into position, and the process is repeated until all the bolts are inserted. The slide then retracts, and the part is manually ejected.
For maximum strength and rigidity, Joraco Press constructed the press from a combination of cold rolled steel and tool steel. With a footprint of only 45.0″ long x 24.0″ wide, the machine occupies just 7.5 square feet of floor space. A safety light curtain was integrated that protects operators from injuries related to machine motion. To learn more about this system or our custom solutions for product assembly, contact Joraco Press Company directly.
Riveting
Rivets are permanent fasteners that feature smooth cylindrical shafts with a head on one end. Manual installation requires the use of pre-punched or pre-drilled holes into which the rivet is inserted. Once it is in position, its exposed end is hammered to secure it in place. Riveting press machines serve as a modern alternative to manual riveting, allowing for easier, faster, and more consistent installation. They are available in many variations—such as manual feed or automatic feed—to suit different manufacturing applications. For Riveting Applications, we provide tubular/eyelet rivet machines built around our standard line of TOGGLE-AIRE® Series Pneumatic Presses. These machines offer the same reliability and ease of maintenance expected of us and give customers the convenience of interchangeable parts between the rivet machines and pneumatic press line.
Staking
Staking Workstation for Supplier of High Quality Laser Engraved Pet ID Tags
A supplier of high-quality laser engraved pet identification products approached Joraco Press Company about the possibility of furnishing a turnkey staking system for the forming of anodized metal into several specific dog tag profiles.
This turnkey workstation incorporates a staking press with custom tooling; a servo-powered rotary indexer and an air driven ejection system. After the operator loads blanks onto a rotary indexer with custom nests for each of the seven different profiles, the indexer moves the parts under the press where they are staked. Staked parts rotate to the ejection station where they are blown out of the nest by a pneumatic cylinder and into an ejection chute.
We built this automation system for continuous duty operation. At the customer site, it runs 24 hours/day for the mass production of pet identification tags with overall dimensions of 2.5″ in diameter x 0.1″ in thickness. The servo motor on the rotary indexer allows for flexible, high accuracy positioning to obtain repeatable accuracy of ±0.001″ on the finished tags. The customer was so impressed with the speed, accuracy, and repeatability of this system that they placed an order for four additional machines.
Swaging
See MoreCalibrating
See MoreCompressing
Joraco Press Company Manufactures a Hydro-Pneumatic Press for Use in the Pyrotechnic Industry
Joraco Press Company, a premier manufacturer of pneumatic presses, was approached by a company well-known in the pyrotechnic industry to provide a press that would enhance the production of their unique product line. This particular application called for the ability to compress volatile material within a form to a specific density. This is not the first time that an Joraco Press was chosen for an application that called for the compression of explosive material and they were excited to gain more exposure in this field.
Joraco Press's HYDRO-AIRE Series offers clean, reliable and accurate results with presses ranging in capacity from 4 to 30-tons of force. This air-over-oil series is a much cleaner alternative to a hydraulic press and offers the same advantages. It is fully contained with no fluid reservoirs or hydraulic lines, and features rapid advance with an automatic power stroke.
The customer was pleased with the arrival of their 8 ton HYDRO-AIRE Series Model HP8 press. Not only was it delivered in the nick of time, but it also worked out of the crate just as it was intended to do. They received our press with a narrow window of time before they were schedule to meet with clients to test the manufacturing process utilizing it, but their confidence was assured quickly upon its arrival at their facility. Much like our customers, Joraco Press Company also strives to produce high quality products that perform as advertised.
Cutting
See MoreFastening
See MoreHeat Stamping
See MorePress-Fit
Punching
Joraco Press Company used its TOGGLE-AIRE Series Model 3530 pneumatic toggle press and a custom designed punch tool set to help a client with their sheet metal sample packs. Using 2" infeed material up to 24g galvanized steel or .040" aluminum, operators can stamp 2" x 3.5" card sized samples with 1/4" rivet holes to combine a variety of samples. No hydraulics! No electronics! Just a simple air feed and benchtop space. While this version is manually fed with pre-cut stock, the press can easily be combined with feeders, decoilers, and straighteners for automatic punching needs!
VIDEO BELOW
Shearing
Joraco Press Company's Punch & Shear Application Using Servo Driven Feeder
Joraco Press designed and built the fully automated multi-press punch and shear system for the manufacturing of transformer core sheets. It featured two high-accuracy 10-ton TOGGLE-AIRE® Series Model 2530 pneumatic presses, one for punching the hole and the other for shearing the sheet. The primary challenge of this project involved obtaining precise tolerances of ±0.002″ around the burr of the punched hole on the steel sheet. To ensure dimensional accuracy in the customer’s stack core transformer design, our engineers had to design, build, and exhaustively test the punch tools to ensure they repeatably produced holes with the correct size and shape.
Constructed from cold rolled steel for strength and rigidity, the automated punch and shear system features a space-saving 29.5″ long x 30.75″ footprint. Along with the two presses, it incorporated a servo feed that delivers precise positioning accuracy and enables the press to produce consistent parts with close tolerances at fast operating speeds. The punch and shear system also included an integrated PLC system that was fully programmed and ready to run as soon as the customer loaded up the material.
Joraco Press Company supplied this automated fabrication system with a precision sharpened carbide tooling package. The tooling successfully obtains precise tolerances, and with carbide’s ability to maintain its cutting edge, even during high speed punching, it produces accurate parts over long production runs.
Marking
Vintage Joraco Press TOGGLE-AIRE® Series Marking Press on Science Channel's How It's Made:
Stamping
Are you ready to discuss your Application?
Joraco Press Company has Engineers and Project Managers on hand to help evaluate your project. Feel free to schedule an online meeting or visit our Headquarters in Smithfield, RI!
OUR CUSTOMERS
Our customers produce almost every kind of industrial, commercial, and consumer product available in the world market. These customers, and hundreds more, put their trust in Joraco Press Company's reliability, precision and factory direct service - so can YOU!